JoeyD23
#utvunderground
PRODUCT SPOTLIGHT: MINOTAUR SUPER DUTY AXLE
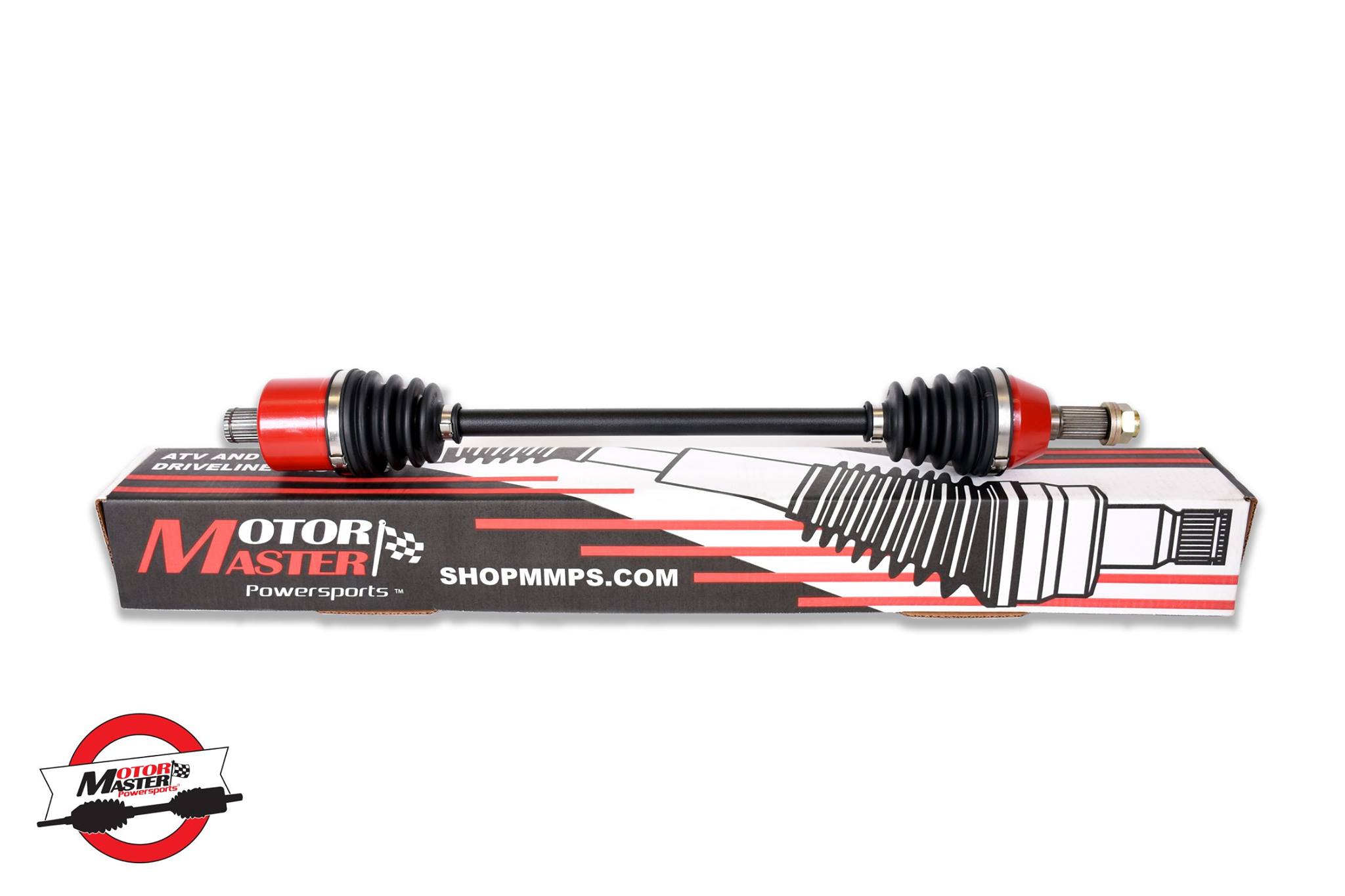
Motor Master Powersports are proud to announce the official launch of their new Minotaur Super Duty Axle line. This axle is the next evolution in axle performance as it is designed for BIG wheels and BIG power!
Minotaur Super Duty Axles feature robust CV housings, bars, cages, and races. Produced with ultra-strong chromoly steel to provide TWICE the strength of OEM axles (*tested using in-house calibrated machinery). Additionally, our proprietary top secret heat treat process is used on the entire assembly to ensure ultimate strength in areas vulnerable to breakage.
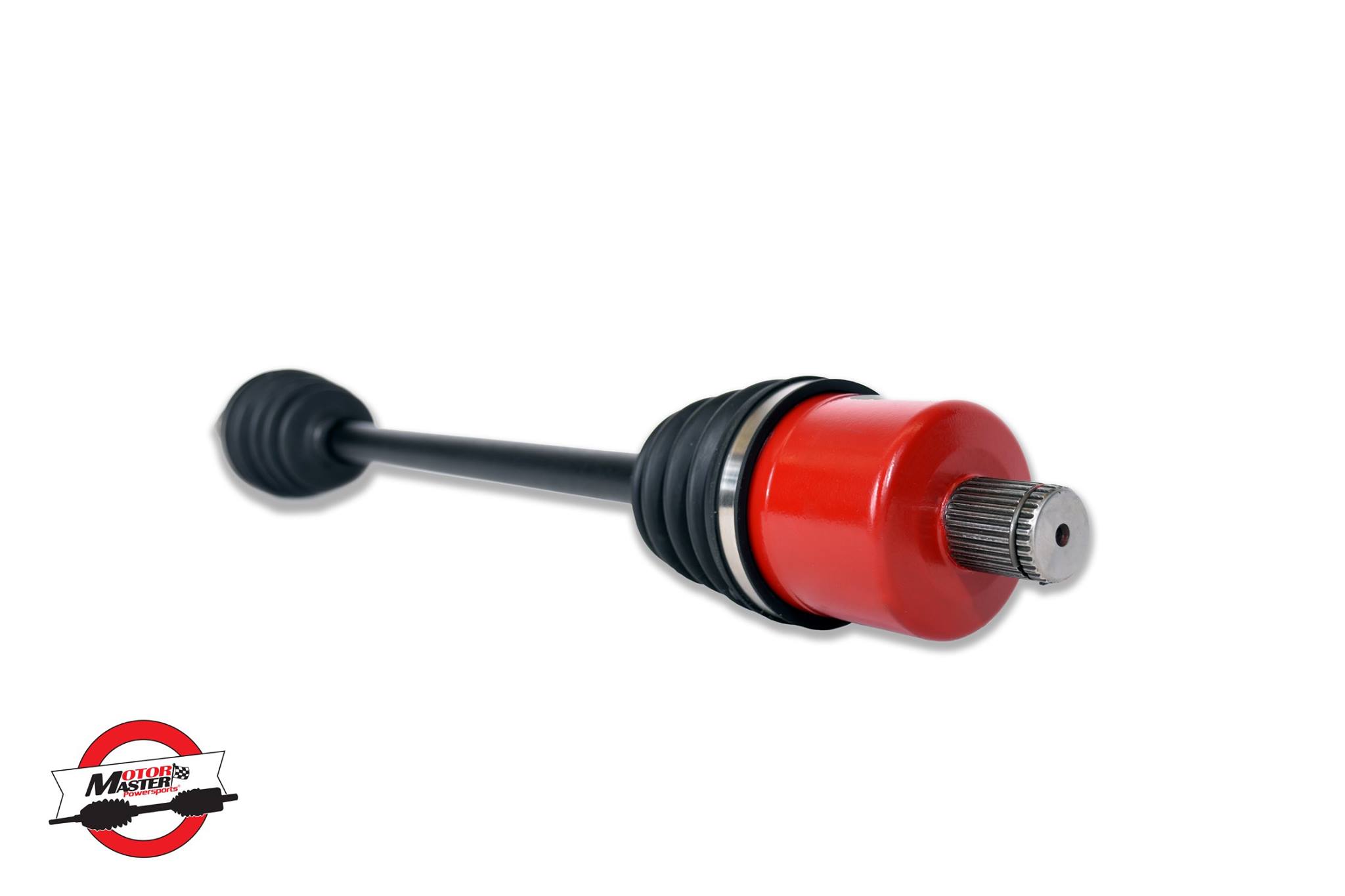
Increased Operating Angle- OEM axles were not designed to continually operate at the severe angles created by suspension lifts. Minotaur CV joints handle these conditions with ease by allowing 40 degrees of articulation. Designed to slide on the bar splines that will provide 2” of overall travel to work on any terrain, Minotaur Axles are the ideal choice for ATV’s and UTV’s with lift kits or extended A-arms.
Minotaur’s Look as Good as They Perform- Minotaur CV joints are protected from dirt and contaminants by Motor Master’s exclusive Dura-Boot. Our Dura-Boot is made in-house from a blend of special thermoplastic materials that will withstand the most severe trail and temperatures. Dura-Boots are super-durable, super long lasting and with our Husky HTS-2 moly performance grease, you get the best protection in the industry!
These Minotaur Super Duty Axles, like the Dura-Boots, are made in the U.S.A. by Motor Master Powersports. So, if you have a lifted ATV/UTV or want to run with the highest quality axle out there, the Minotaur Axle will fit your needs!
For more information, the list of Minotaur applications and specs, and to view Motor Master Powersport’s extensive driveline coverage, visit www.shopmmps.com
About Motor Master Powersports:
Motor Master Powersports is a division of Aircraft Gear Corporation. A family owned business group that has been in operation for over 60 years, and includes Rockford Constant Velocity one of the largest manufacturers and distributors of CV parts in the Western Hemisphere.
Motor Master’s specializes in the manufacture and distribution of complete CV axles, CV half shafts, CV joints, Duraboot CV boots, CV rebuild kits, and universal joints for the ATV, UTV, Work Utility (John Deere, Kubota etc.) and Japanese Mini-trucks market. Motor Master Powersports provides the most complete driveline coverage in the aftermarket!
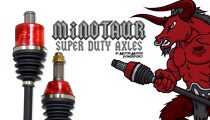
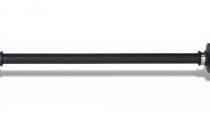
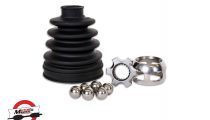
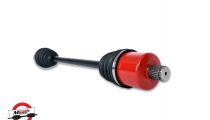
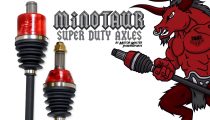
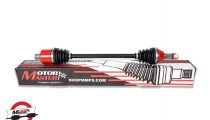